Interview: Jay Schabel, President of Brightmark Energy Plastics Division
We are inspired by people who are passionate about technology that solves pressing global challenges. Scaling and commercializing those solutions requires serious knowledge, courage, support, and perseverance. In this interview series, our chief actuary, Sherry Huang, talks with friends of NER who demonstrate these qualities professionally and personally, and whose journeys will inspire you, too.
NER worked closely with RES Polyflow to ensure the cost-effective capitalization of its plastics waste-to-value facility in Ashland, IN, USA. Brightmark Energy acquired a majority stake in RES Polyflow in November 2018. This interview has been lightly edited for length and clarity.
Jay is a calm, wise, and thoughtful business leader and technology entrepreneur. Before we first met, I joined a conference call for which I hadn’t yet received background information. Although he was leading the discussion and I had not initially been invited, unprompted, Jay sent me the files that I needed to get up to speed. It was a small act of kindness, which made an everlasting impression, and I knew then that RES Polyflow was in good hands.
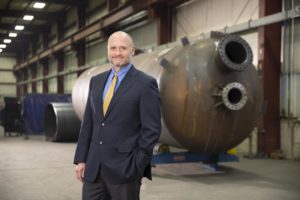
Jay, let’s start with how you got to where you are today. You have vast engineering and construction management experience. Tell us about how you started your own businesses and how that took you to Brightmark Energy today?
I always knew I would start my own business. My father owned a successful trucking company, and I wanted the same experience of creating something. I launched my first start-up on January 1, 2000: a technology company that makes metal injection molding machines. That company is still operating and profitable today! I sold it when I bought another company in the automobile industry with some friends. In the next eight years, I bought and sold various companies, building up to an organization with $300M in revenue before selling my interest to my partners in 2008. This process of buying, building, and selling businesses provided great training for my work with RES Polyflow. I started on the plastic conversion technology in 2008. It was originally known as Polyflow until we added ‘Renewable Energy Solutions.’ Since our acquisition, we are Brightmark Energy Plastics Division, and we are still thinking of a name for the core technology.
Brightmark Energy Plastics Division is providing an important technology solution that turns post-use plastic into valuable products, and this reduces the amount of waste that would otherwise end up in a landfill or the ocean. Looking forward five to 10 years, what is your vision for this technology?
We want to divert 8M tons of plastic waste from landfill and waterways by 2025 and are already working on initiatives to support this goal. (Editor’s note: The Ocean Conservancy estimates that 275M tons of plastic waste is produced every year, of which 8M tons enter the oceans annually.)
What are some trends you are seeing in your industry? How do you see your industry changing and evolving?
The goal of our industry is to figure out how we can help divert as much plastic waste as possible from landfill and waterways. Recyclers are struggling to figure out what to do since China and southeast Asian countries stopped accepting used plastic from foreign countries. We want to use our disruptive technology to help manage this change and solve this plastic waste pollution problem.
Others have been working on this issue for a while, too. For example, Dow Chemical along with its partners have tested two “Hefty Energy Bag” programs in Omaha, Nebraska and Citrus Heights, California. They collected previously non-recycled plastics and converted them into valuable products, demonstrating that recovery of non-recycled plastics is a viable municipal process.
What advice do you have for technology entrepreneurs who are trying to start or scale their business?
Be honest with yourself. At RES Polyflow, we determined that we needed a significant level of scale in order to be economically viable, but that created a difficult financing task. The insurance solution from NER and AXA XL was critical in completing the debt financing. The required level of financing was a big pill to swallow, but at the end it was beneficial. Make the tough decision early and stick with it.
Lastly, I understand you used to own and operate a winery, which is almost as exciting as reducing waste and pollution for planet Earth! Outside of Brightmark Energy, what are you up to now?
Yes, my wife and I used to own three acres of grapes. We made our own wine and operated a winery, but it became too much while I traveled a lot for RES Polyflow so we sold it a while ago. Now we are building our dream home. We are having the time of our lives!
Thank you, Jay!
About the Plastics Renewal Facility in Ashley, Indiana
Brightmark Energy’s plastics-to-fuel pyrolysis process sustainably recycles plastic waste directly into useful products like fuels and wax. The plastics renewal facility, now under construction, will convert 100K tons of plastic into 18M gallons of fuel and 6M gallons of wax annually. To finance this deployment, RES Polyflow and Brightmark Energy raised an aggregate $260M including $185M in Indiana green bonds, underwritten by Goldman Sachs & Co.
###