A Primer on Pyrolysis
By Brad Price, P.E.
New Energy Risk helps accelerate the commercialization of industrial technologies that are solving global challenges. One of the technology platforms that we review frequently is pyrolysis. This important process contributes to a circular economy, and we are proud to help our clients bring it to commercial scale. This is Part 1 in our series that takes a closer look at innovations changing our world.
What is Pyrolysis?
A Dictionary of Chemistry defines pyrolysis simply as “chemical decomposition occurring as a result of high temperature.” (1) In practice, pyrolysis technology is a family of technologies based on pyrolysis chemistry. Pyrolysis chemistry is simply what happens to a material (in solid, liquid, or gaseous state) when it is heated in the absence of oxygen. Molecules start to “crack” when heated to high temperatures, which means they start to spontaneously break apart and recombine in random and yet somewhat predictable ways. No additional ingredients like catalysts or initiators are required, although they can enhance the process. Pyrolysis is used to upgrade a lower value material into a higher value material; depending on the feedstock, it is sometimes referred to as a “waste to value” process.
Is Pyrolysis New?
Not at all! Pyrolysis chemistry is core to several of the largest and most important industrial processes in the world.
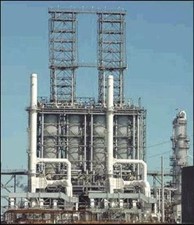
A great example is ethylene. Ethylene is produced using pyrolysis chemistry and is considered the world’s most important chemical as it is needed for the production of products as diverse as industrial chemicals, specialty glass, metals, food, medical anesthetics, refrigerants, rubber, and much more. (2) It is forecast that ethylene production will be 202.9 million metric tons by 2026, more than any other organic chemical. (3) Ethylene is made from a variety of hydrocarbon feedstocks (e.g., ethane, propane, naphtha) primarily using steam cracking furnaces. These furnaces are giant, fired tubular reactors that operate in the range of 1400 to 1600 °F (~750 to ~875 °C), with a gas residence time of 0.1 to 0.5 seconds to complete the conversion! (4)
Examples of pyrolysis products and technologies include pyrolyzing wood to produce one of America’s favorite backyard barbecue fuels: charcoal. [1] In an oil refinery, one of the largest and most visible units is the coker unit, which also utilizes pyrolysis chemistry. [2]
What is New About Pyrolysis?
There is tremendous change happening with pyrolysis. Generally, feedstock is the key focus area NER has seen innovating. There are many feedstocks that had never been used successfully at commercial scale in a pyrolysis process but that are coming to fruition today.
An example of a new feedstock is waste plastic. Many innovators are attempting to commercialize waste plastic pyrolysis processes to produce liquids and gases that are then used to produce new “virgin quality” plastic. These output plastics, which have been “chemically recycled,” are molecularly identical to regular plastic and have advantages over more traditional “mechanically recycled” plastic in that there is no compromise on the material properties of the plastic. I have witnessed this process firsthand because I was part of my previous company’s first successful commercial trials to process waste plastic pyrolysis oil through steam cracking furnaces to produce ethylene.
Pyrolysis is also being applied to biomass feedstocks made from residual agricultural wastes, for example. The liquids produced from biomass ultimately qualify as biofuels and can be extremely attractive to customers looking for a more carbon-conscious fuel. Pyrolysis oil from biomass has very different properties than the oil produced from waste plastic, and has different properties depending on the biomass material being pyrolyzed. These properties do not allow the pyrolyzed oil to be used directly as a transportation fuel; this is a challenge that has and will continue to require significant innovation.
What Does Pyrolysis Produce?
In general, pyrolysis produces three products: a solid, a liquid, and a gas. The ratios of these three products depends primarily on the reaction temperature and the feedstock being processed.
- The solid is oftentimes referred to as coke or char. It is carbonaceous and has a similar appearance to coal or black powder. Depending on the properties of this material, it can have many uses, such as for carbon black (for pigmentation and tire rubber strengthening), for soil enhancing, or as a fuel source.
- The liquid is a broad boiling range product, like crude oil. The oil has distinct properties that make it very different from fossil crude oil, and those properties depend on the material being pyrolyzed and the operating conditions (temperature, pressure, and residence time) of the pyrolysis reactor. Generally, this liquid must go through several upgrading processes prior to being used as a transportation fuel or a chemical intermediate (as is also true for fossil crude oil).
- The gas product is non-condensable and goes by many names such as syngas or cracked gas. Common molecules found in this gas include hydrogen, methane, carbon monoxide, carbon dioxide, ethylene, and propylene. This gas can be recovered for fuel or sold as a chemical feedstock to other industrial processes.
Pyrolysis falls on a spectrum of similar thermal deconstruction chemical processes, including torrefaction, slow pyrolysis, fast pyrolysis, and gasification. They are shown below, organized by the temperature ranges they typically fall in.
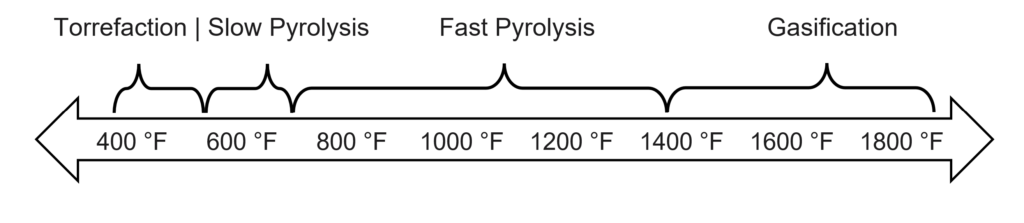
The product distributions for each of these categories are shown below. Keep in mind that these are very generalized and can vary significantly depending on the feedstock, operating temperature, pressure, and residence time of the feedstock in the reactor.
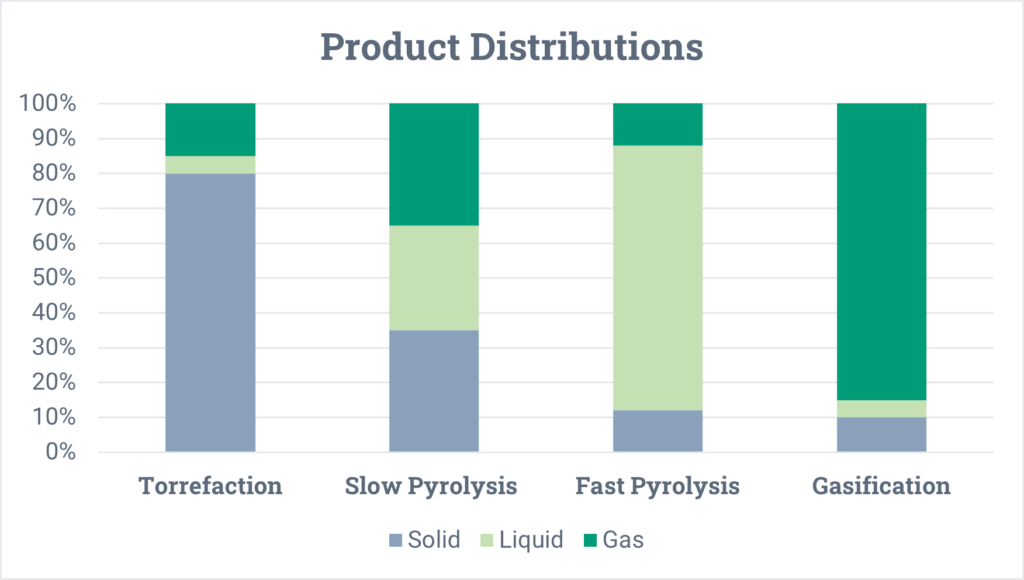
What Is the Business Case for Pyrolysis?
Pyrolysis is always an upgrading process, meaning it transforms lower priced feedstocks into higher value products. The products are generally base chemicals or fuels and not as highly valued as specialty chemicals (there are exceptions). The business advantage of pyrolysis is usually related to feedstock. A low cost or otherwise strategic feedstock is where pyrolysis really shines.
For example, waste plastic feedstock is generally low cost, and may even result in the processor receiving tipping fees (getting paid to take feedstock!). In addition, the product can be certified as recycled material, which demands a premium in the marketplace. When the recycled pyrolysis products are then used to produce new plastic, that plastic product can be certified as recycled, or circular, too.
Similar business cases exist for biomass as a feedstock for pyrolysis. The material may be low-cost waste streams from other industrial or agricultural processes. The resulting liquid then qualifies for biofuel credits that then receive a Renewable Identification Number (RIN) and/or qualify for the Low Carbon Fuel Standard credits, which can be extremely lucrative.
What Are the Challenges for Pyrolysis?
Innovation in the process industry is challenging. To design a reliable (and profitable) process, technology developers must identify and mitigate many issues that are unique to each technology. Unfortunately, innovative technology projects frequently fail. Even with proper piloting, innovative process technologies on average only achieve ~80% of the design production rate six months after startup. Without proper piloting, this number is closer to 50%. (6)
The first challenge area for pyrolysis is solids handling. Solids handling can be the bane of an innovator’s existence. While mundane, it oftentimes causes significant reliability issues. The solid char product is oftentimes sticky or otherwise hard to convey and can cause mechanical problems due to buildup on the inside equipment. Established industry processes handle the solid byproduct by either periodically air burning it inside the reactor, or by mechanically removing it from the reactor. Spare equipment is oftentimes required to handle the outage time associated with these activities.
Product quality is another challenging area for pyrolysis innovators. The liquids and gasses produced can be very different from produced by typical fossil-derived processes, and it may be difficult to find customers that are able to receive such a feedstock product. These feedstocks can be full of contaminants, and the resulting product can be acidic and unstable. Many customers will require significant quantities of product to test it, qualify it, and establish contractual acceptance criteria. Upgrading of the liquids can be equally challenging and requires significant development work to ensure the upgrading equipment is compatible with the properties of those liquids.
How Can New Energy Risk Help with Your Pyrolysis Process?
Financing an innovative pyrolysis process can be a challenge, due to the risks associated with innovative technology. NER is positioned to provide performance insurance solutions to protect capital providers if the technology does not perform as expected. NER’s in-depth diligence process and innovative technoeconomic modeling allows us to quantify the risk associated with projects deploying these technologies. We have over a decade of experience enabling developers to de-risk their project and attract capital at terms that are impossible to achieve without insurance.
An example pyrolysis client of ours is Brightmark, which is currently finishing construction of their flagship waste plastic pyrolysis facility in Ashley, Indiana. NER was able to assist Brightmark by helping to provide a performance insurance solution to protect bondholders in their project debt financing. In 2019, Brightmark was able to secure $185 million in debt capital (bonds) at a low 7.125% interest rate, in part due to NER’s insurance solution.
Pyrolysis is just one example of the innovative technologies that we evaluate and support at NER. This is Part 1 in our series that takes a closer look at some of these innovations. Next up: A Guide to Gasification.
[1] The ubiquitous backyard grilling product we call charcoal is produced using pyrolysis chemistry. Modern production of charcoal is not much different from how it was produced anciently and requires temperatures around 750 °F (~400 °C).
[2] The global refinery coking capacity is around 9,603 million barrels per day (8). These massive units upgrade some of the heaviest oils in a refinery into gasoline, diesel, and other more valuable fuels using pyrolysis chemistry. They operate at temperatures around 900 °F (~500 °C).
Works Cited
- Daintith, John, [ed.]. A Dictionary of Chemistry. Sixth. Oxford/New York : Oxford University Press, 2008.
- Kaskey, Jack. Harvey Has Made the World’s Most Important Chemical a Rare Commodity. Bloomberg. [Online] August 31, 2017. https://www.bloomberg.com/news/articles/2017-09-01/world-s-most-important-chemical-made-rare-commodity-by-harvey.
- Research and Markets. Global Ethylene Production Capacity & Demand Markets, 2022-2026: Rising Production Capacity of Ethylene Dichloride, Growing Petrochemical Industry, & Increasing Demand for Bio-based Polyethylene. Cision PR Newswire. [Online] February 07, 2022. https://www.prnewswire.com/news-releases/global-ethylene-production-capacity–demand-markets-2022-2026-rising-production-capacity-of-ethylene-dichloride-growing-petrochemical-industry–increasing-demand-for-bio-based-polyethylene-301476354.html.
- Murzin, Dmitry Yu. Chemical Reaction Technology. Berlin/Boston : Walter de Gruyter GmbH, 2015.
- Lindstrom, Jake K, et al. Condensed Phase Reactions During Thermal Deconstruction. [ed.] Robert C. Brown. Thermochemical Processing of Biomass. Second. Chichester : John Wiley and Sons Ltd, 2019.
- Andras Marton, Ph.D. Getting Off on the Right Foot – Innovative Projects. Independent Project Analysis Newsletter. March 2011, Vol. 3, 1.
###